The pressure transmitter should be inspected and prepared before use for the first time (for example, when the isolation liquid needs to be used, the isolation liquid should be poured into the corresponding instrument, and the air bubbles should be cleaned at the same time). After the initial pre-start preparation is completed, it is necessary to preheat up the power supply for a period of time and then open the impulse valve smoothly to prevent the impulse valve from being opened too violently, resulting in a sharp increase in the internal pressure of the pressure transmitter and damage to the sensitive components.
It should be noted that the differential pressure transmitter is filled with isolation liquid in the instrument before use and then migrated to ensure that the output meets the specified requirements. In addition, after the installation of the differential pressure transmitter is normal, and the three valve groups are in a closed state, the process of opening the primary impulse valve ➝ opening the balance valve ➝ opening the high-pressure valve ➝ shutting down the balance valve and opening the low-pressure valve can be opened.
- (1) Confirm the installation size
Before installing the pressure transmitter, use measuring tools such as aperture measuring instruments to confirm whether the size of the mounting hole is appropriate, and reaming should be carried out if the mounting hole is found to be small, so as to prevent the mounting thread from being extruded and worn and affecting the sealing of the pressure transmitter or causing damage to the internal components.
- (2) Clean the mounting holes
The main purpose of cleaning the mounting holes is to prevent foreign objects from clogging and affecting the normal operation of the pressure transmitter. The pressure sensor on the barrel of the pressure transmitter should be temporarily removed before the foreign object is cleaned to prevent damage from foreign bodies. It should be noted that in the process of removing the pressure sensor, it is necessary to prevent the melt from entering the mounting hole, so it is easy to cause damage to the top of the pressure sensor caused by overpressure during the installation process after the melt enters the installation hole.
(3) Reasonable selection of installation location
If the sensor element in the pressure transmitter is installed too close to the front of the production line, the top of the sensor is easily damaged by the wear of unmelted materials. If the sensor element is installed too close to the back of the production line, the molten material may accumulate between the mounting screw of the pressure transmitter and the sensor element and degrade to a certain extent, which will also lead to the distortion of the collected pressure signal. If the selected mounting position is too deep, the pressure sensor end at the front of the transmitter may fail due to compression damage.
(4) Clean thoroughly
The extruder barrel needs to be fully cleaned before installing the pressure transmitter, and the most common cleaning methods are mainly chemical cleaning agents or using a wire brush. It should be noted that cleaning with a detergent or with a wire brush can easily damage the diaphragm of the internal sensor element, so the sensor element needs to be removed before cleaning. In addition, when the barrel is heated, the sensor element needs to be removed before the top of the barrel cleaned with a soft cloth, and the sensor holes should be adequately cleaned with appropriate tools.
(5) Pay attention to waterproofing
At present, most pressure transmitters take into account the influence of humid arc welding machine in circuit design, but because the pressure sensor element itself has certain requirements for the humidity of the working environment, it is necessary to pay attention to the environmental humidity should not be too large before installing the pressure transmitter. If it is not possible to keep the environment sufficiently dry under some special conditions, a special sensing element with good waterproof function is required.
(6) Pay attention to the influence of low temperature
Although some of the sensor elements inside the pressure transmitter are well resistant to low temperatures, the ambient temperature is too low and the sensors inside the transmitter may be damaged. For example, if the fluid inside the inducer expands due to low temperature condensation in a pressure transmitter installed in an uninsulated environment, the sensor may be damaged due to over-pressure.
(7) Avoid pressure overrun
In order to increase the reliability of the operation, the pressure transmitter adopts the concept of redundancy, and usually a small pressure overrun does not directly cause damage to the hardware. However, if the pressure exceeds the limit too much or the overload frequency is high during use, it is still easy to cause the failure of the pressure transmitter. Therefore, the range of the pressure transmitter should be selected according to the actual working conditions to ensure that the range of the pressure transmitter is greater than the pressure of the working environment.
In addition, in terms of inspection and verification, a functional inspection should be carried out once a week, and an accuracy verification should be carried out once a month, and attention should be paid to removing the attached dust in time during the inspection and verification process, and the output current value of the pressure transmitter should be calibrated to ensure that the output of the converter is isolated from the strong current to reduce the interference of the external strong current environment.
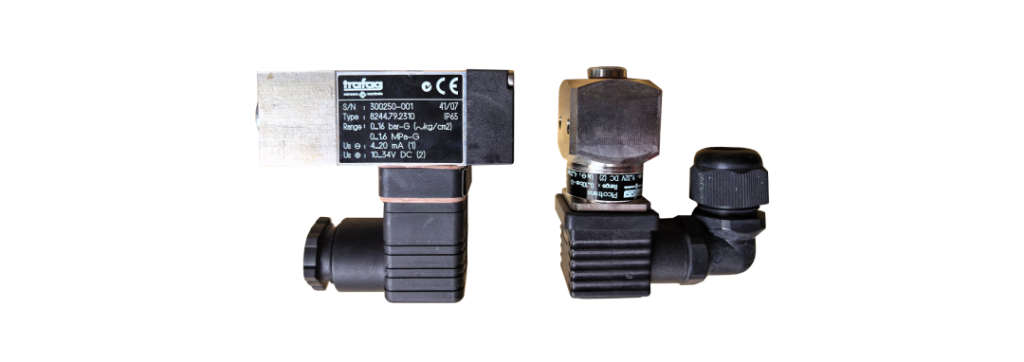
Sensors, Switches & Appliances – Our Recommendations
Qinhuangdao Sino-Ocean Marine Equipment & Machinery Co., ltd. announced inventory information, including temperature sensors, pressure transmitters, electronic level switches, limit travel switches, angular position transmitters, pressure converters, 5/2 – way valves, solenoid valves, float level controllers and many other products.