Two Wärtsilä 8L46C main engine exhaust gas booster system on a ship use booster air bypass valves and wastegate valves to improve the efficiency of the supercharger and improve the working condition of the main engine.
The abnormal opening of the bypass valve seriously affects the normal operation of the main engine and endangers the safety of the ship.
The pressurized air bypass valve is abnormally opened
- 1. Fault phenomenon
One day, the right host of a ship could not reach the rated power under high load, the average exhaust temperature exceeded 450 °C and an alarm was given (the normal exhaust temperature of the main engine should be lower than 430 °C), the booster pressure of the main engine increased, the exhaust smoke turned black, the scavenging temperature rose, and the inspection found that the booster air bypass valve was abnormally open.
- 2. Failure hazards
The main engine works under high load, the booster air bypass valve is abnormally opened, the exhaust gas pressure is greater than the scavenging pressure, the high-temperature exhaust gas enters the scavenging box, mixes with the fresh air after pressurization into the cylinder, and mixes with fuel for combustion.
The entry of exhaust gas leads to a serious shortage of fresh air, because the exhaust gas contains a large number of nitrogen and sulfur compounds, which reduces the oxygen content in the inlet air, the combustion deteriorates, and the phenomenon of flame retardation occurs, resulting in an increase in exhaust temperature, which directly affects the life of the exhaust valve.
At the same time, part of the exhaust gas enters the scavenging box, which affects the amount of exhaust gas entering the exhaust gas turbine and reduces the speed of the exhaust gas turbine.
The speed of the compressor on the coaxial unit is reduced, further reducing the air intake.
The high-temperature exhaust gas mixes with the fresh air after pressurization, resulting in an increase in the temperature of the pressurized air; The entry of high-temperature gas leads to the high-temperature aging of the valve seat and valve line of the intake valve, and finally causes the intake valve to be closed loosely, and in serious cases, the valve spring is broken.
- 3. Fault solving
Dismantling of the booster air bypass valve found that the spool diaphragm of the solenoid valve was damaged, resulting in the inability to shut down between pipeline A and pipeline B.
After the solenoid valve is replaced, the fault is solved.
- 4. Countermeasures
Regularly perform functional tests on the booster air bypass valve to ensure that the equipment is in good condition.
(1) When the main engine is stopped, the booster air bypass valve should be closed, and there should be no voltage on the terminal connected to the pressurized air bypass solenoid valve in the junction box; Visually inspect the butterfly valve disc position with the actuator to see if the position indication position corresponds to the actual position.
(2) Connect the pressure sensor inspection tool to the inspection port 6.
Slowly increase the pressure and check that the pressure switch is on at 0.35bar.
At this point, 24V DC is on the terminal connecting the charge air bypass valve in the measurement junction box, indicating that the charge air bypass valve is open.
The functional test of the exhaust gas booster system is shown in Figure 1.
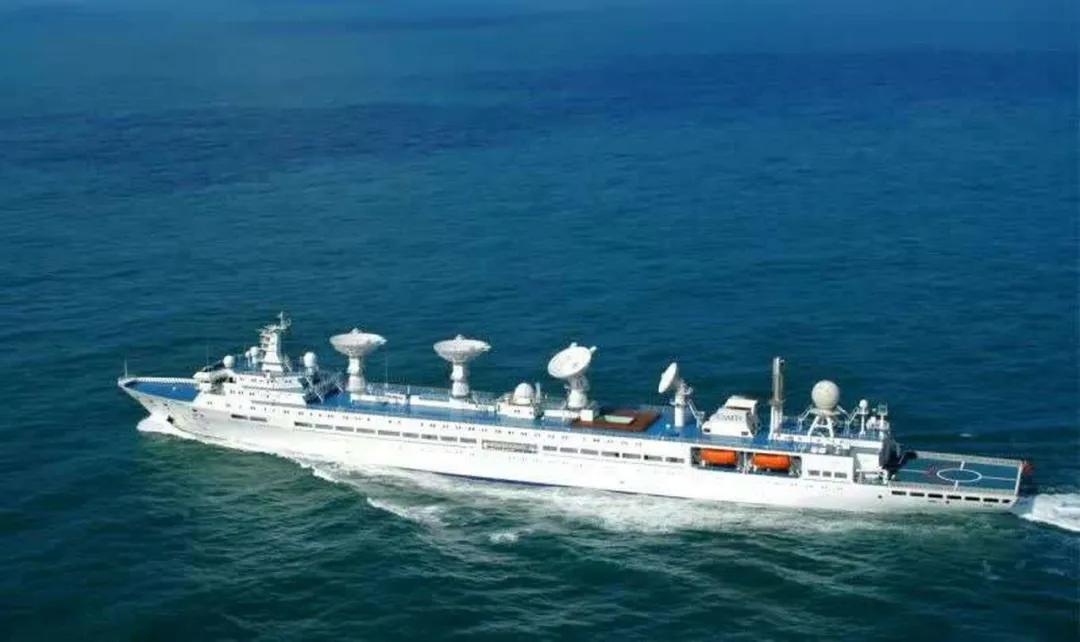
Main Engine Exhaust Gas Booster System Fault Analysis And Troubleshooting-Part 2