Twin-screw pumps are widely used on ships. Due to their characteristics such as smooth liquid transportation, low vibration, low noise, strong self-priming ability, wide range of conveying media, and long service life, they are mainly used for the transmission of fuel oil, lubricating oil, and various chemicals. Considering that light fuel and chemicals are flammable, explosive, and highly harmful to the human body, twin-screw pumps are required to operate without leakage. The requirements for bearing temperature during the operation of a twin-screw pump are relatively high. Generally, the bearing temperature after the repair of a twin-screw pump cannot exceed 70 degrees Celsius. From the perspective of ship repair, this article sorts out the repair items of twin-screw pumps during the repair period, hoping to provide some reference for marine engine managers.
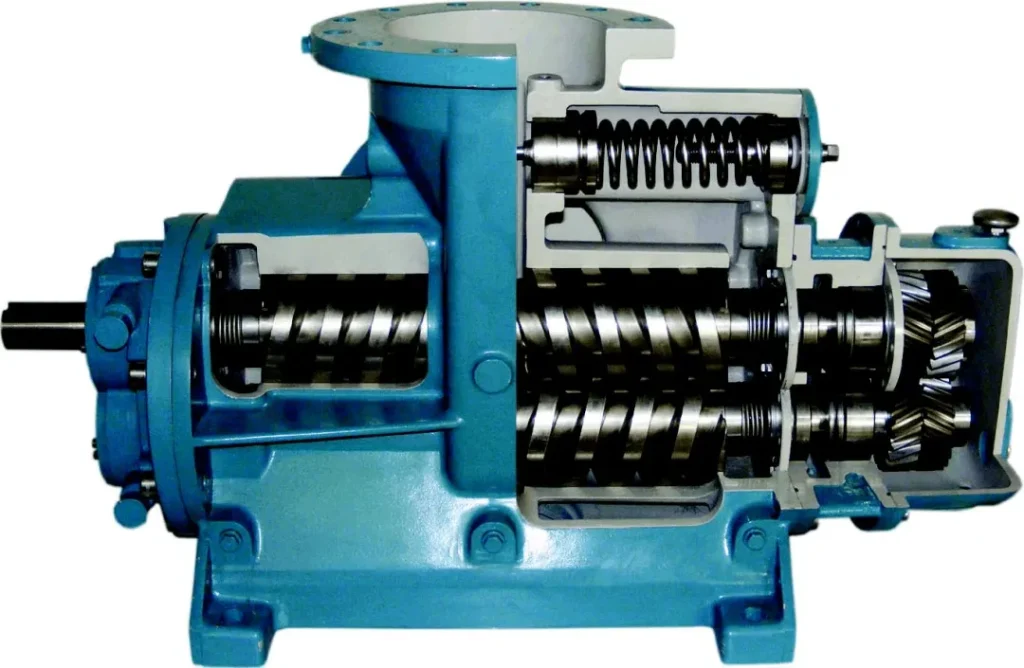
1. Preparation before the repair of the Twin-screw pumps
Preparation before repairs is crucial.
First read the twin-screw pumps manual and related parameters carefully.
Combined with the use and maintenance records of the twin-screw pumps, if conditions permit, the pump can be started before dismantling and checked for operation, which is convenient for intuitive understanding of pump problems and failures.
After grasping the basic operating conditions and faults of the pump to be repaired, a corresponding repair plan is developed, and a suitable repair site is selected.
Do a good job in the security evaluation of the repair and choose the appropriate repair tool.
2. Disassemble the pump and accessories
First, disassemble the pump and its auxiliary piping.
The pump inlet and outlet pipes should be blocked in time to prevent the oil and gas in the pipeline from flowing out, and pay attention to ventilation at the same time.
If the pump is used to transport chemicals, make sure not to touch the liquid flowing out of the pipe when disassembling it to avoid harming the human body.
If you accidentally touch it, wash it immediately with water.
The disassembled coupling nylon rod should be carefully inspected.
If there is less wear and tear, put it away and continue to use, otherwise it needs to be replaced.
If it is found that the nylon rod is seriously worn, it also means that the center line of the twin-screw pumps is not accurate, and pay attention to adjusting the center line when installing the centering.
After the pump is disassembled, the gaskets of the feet should be marked and put away so that they can be used for installation and alignment, or new gaskets should be made according to the thickness of each gasket.
3. Workshop dismantling and maintenance
After the dismantled twin-screw pumps is lifted to the workshop, the dismantling inspection begins.
If the pump is used for chemical transfer, it needs to be rinsed with water to clean the remaining chemicals from the pump before dismantling.
1) Make a mark
Make a mark before disintegrating.
It is necessary to mark the end cover, gear, bearing seat, driven shaft and other positions to avoid wrong installation when installing.
If the screw is double-threaded, special attention should be paid to marking the relative position on the shaft, otherwise it may rotate 180 degrees when installing.
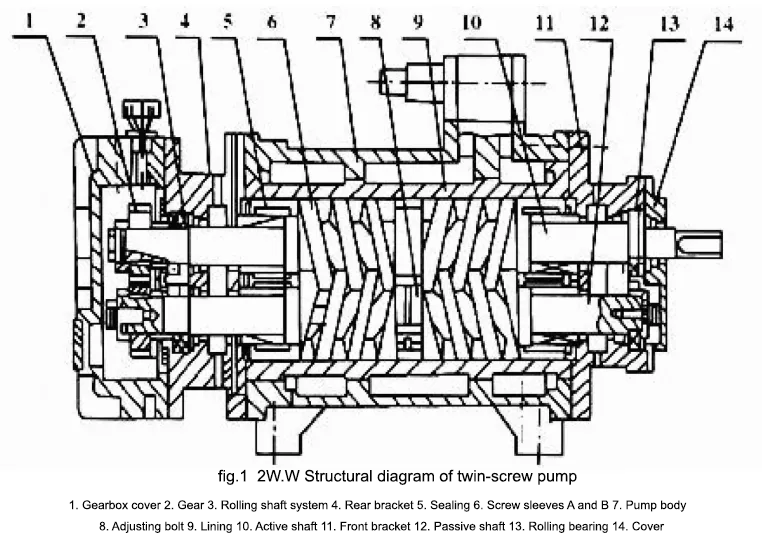
2). Disintegration
After making the marking, disassemble the Twin-screw pumps in order according to the steps in the manual.
Drain the fuel (lubricating) oil in the gearbox, remove the gearbox cover, loosen the gear lock nut, and remove the gear;
Check gear wear.
In general, there will be no problems with the gears.
The fuse of the lock nut needs to be replaced when it is installed.
Once the gear has been removed, the gear end cap can be pulled out along with the bearing.
The bearing is a single row roller bearing with an axially free inner ring.
Due to its large radial load capacity, it is mainly used to bear the radial load of the shaft.
The inner and outer rings of the bearing are loosely matched with the shaft journal and the bearing housing hole, and it is easy to disassemble and assemble.
There is usually an adjustment gasket between the bearing and the gear.
Mark the adjustment gasket and put it away for installation.
This gasket is mainly used to adjust the screw clearance, because the transmission gear is helical.
Disassemble the bearing gland at the input end, remove the bearing lock nut, and eject the end cover of the input end together with the bearing with a screw rod.
The inner and outer rings of the bearing and the journal and the bearing housing bore are interference fits, and the bearing can be destroyed and removed when the screw rod cannot be ejected, but care must be taken to ensure that the shaft and the bearing housing bore can not be injured.
When the end cap is removed, the guide rod should be installed to avoid damaging the shaft seal.
After the end covers at both ends of the pump are removed, the moving ring of the mechanical seal on the shaft of the casing of the pump and the static ring of the mechanical seal fixed on the shaft seat of the pump end cover can be seen.
The seal of the whole pump depends on the four sets of mechanical seals at both ends of the two pump shafts, so when the four sets of mechanical seals are installed, it is necessary to be very careful, and the static ring of the mechanical seal is mostly made of carbon fine material, which is very brittle and easy to damage.
Finally, the two pump shafts are lifted out of the pump body.
Remove the bearing from the pump end cover and remove the shaft seat.
3). Cleaning, inspection and repair
After the pump shaft is removed, the wear of the inner hole of the pump casing and the screw should be checked first, and the gap between the inner hole of the pump casing and the screw should be measured.
If the wear and tear is serious and the gap exceeds the standard, because there is no feasible repair plan and repair value, the whole unit can only be replaced.
If the wear of the pump shaft and pump casing is within the specification, the following repairs are carried out.
Clean and check the corrosion and wear of the pump shaft shaft seal and bearing position.
If the bearing position wears the inner ring of the bearing, and the shaft seal is corroded and affects the seal, it should be repaired with chrome plating.
The chrome plating layer should be guaranteed to have a certain thickness, otherwise the plating layer will easily fall off.
The lathe on the pump shaft measures the run-out.
This is a critical task.
Because if the pump shaft and screw runout are large, it will cause the pump to vibrate and make a lot of noise during operation, and the wear will be aggravated;
At the same time, it will also cause the bearing temperature to be too high in use, which is one of the direct causes of accelerated wear, poor sealing of the shaft seal and shortening of the life of the shaft seal.
Therefore, in the repair process, this work needs to be done regardless of the condition of the pump.
Once the run-out amount is detected, it must be repaired, which is one of the key points that affect the repair quality and service life of the whole pump.
Check whether the lock nut of the screw of the pump shaft is loose, and if it is loose, the nut should be loosened and re-tightened;
If the nut is corroded, it should be replaced with a new nut; If there is corrosion on the thread on the pump shaft, the pump shaft should be repaired.
After loosening the nut, check whether there is looseness between the screw and the pump shaft, if the gap is large, the screw should be removed to check the wear and corrosion of the screw inner hole and keyway, and repair the screw inner hole and pump shaft or replace it according to the situation.
If you need to replace it, it is best to replace the two pump shafts in a complete set, and a single replacement of one screw or one pump shaft will reduce the meshing accuracy of the screw.
Clean and inspect the bearing housing hole, and if it is worn, send it to the outer iron plating for repair.
Disassemble the shaft seal seat for cleaning and inspection to see if there is corrosion and wear, and repair it according to the situation to ensure the tightness.
Professional Insights Into Marine Twin-Screw Pumps Repair – Part II